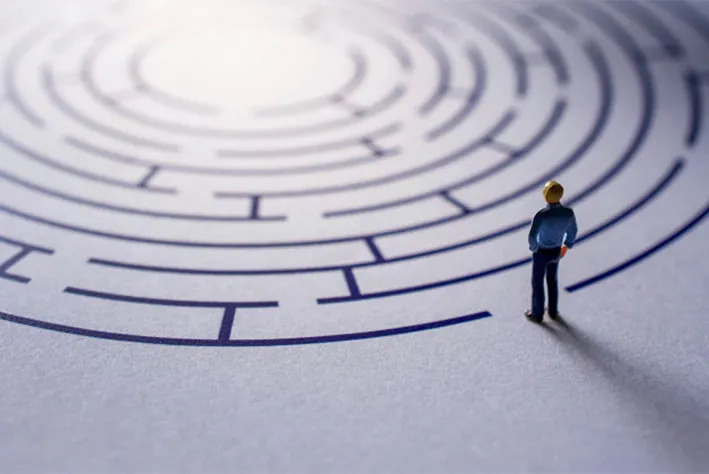
The Requirements
One of their Sea meat division was in an objective to expand their processing capacity so as to meet the rising demands from their buyers globally. This in turn brought them a necessity to improve the storage capacity as well as the handling methodology of the processed goods to handle about 100 tons (Palletized) of meat per day to be stuffed into five 40’ containers which will be replaced from the incoming production lines respectively. The requirement was to provide a storage structure to house 2,500 tons of processed meat designated to 6 cold rooms of size 290 sq.m each at -30°C.
The Solution
The specified cold room dimension thoroughly required higher cubic footprint to store homogeneous goods in order to meet their capacity requirement and the solution is as follows,
- Drive-In Pallet racking system with 4 levels & 3 deep configuration with 2 blocks per room had been offered to store and retrieve pallets following LIFO concept
- All the racking components including the bracings were powder coated so as to endure the cold room temperature of -30°C
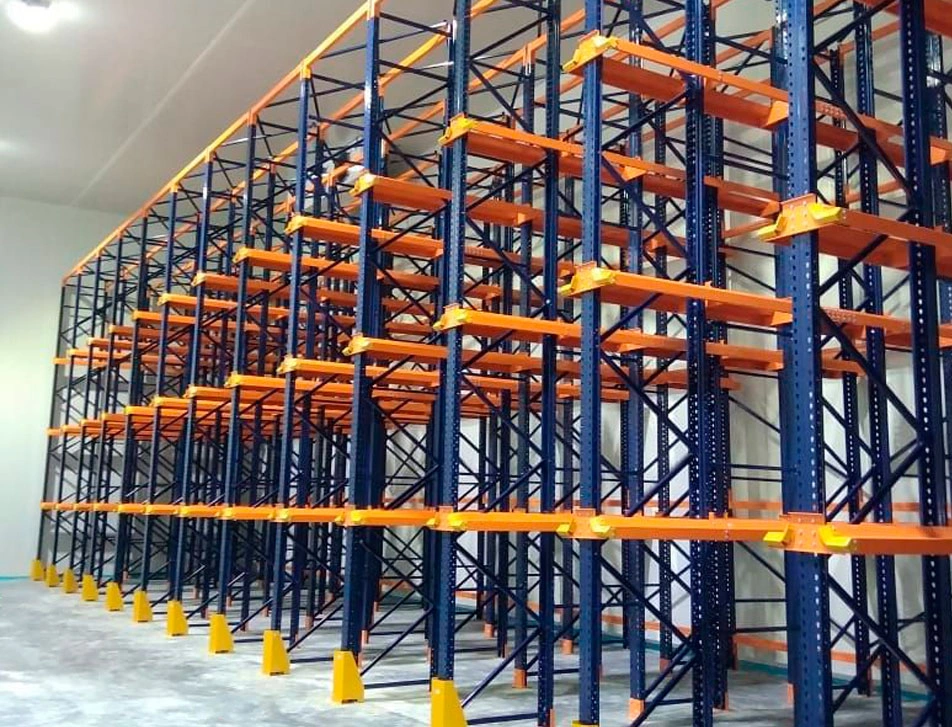
Benefits to the customer
Expected Storage capacity had been achieved by efficient space planning and with the full utilization of vertical height (10m). Drive-In racking enabled them a dimension of dense storage with minimum floor area occupation. The denser storage solution enabled our client to have a considerable savings and advantages in refrigeration consumption. The increased efficiency and productivity of the cold room allowed our client to stuff the expected number of 40’ containers in a day to meet their global demand.
Data and Key figures
- Achieved pallet locations of 2200 nos vs expected 2100 nos
- The racking area housed to about 2,600 MT of processed meat vs expected 2,500 MT
- Effective storage area contribution of 50% from the overall 290 sq.m area per room